Understanding Welding WPS Requirements: Best Practices and Techniques for Top Quality Welds
In the world of welding, understanding Welding Treatment Specification (WPS) criteria is an important component that straight influences the high quality and honesty of welds. As we navigate through the details of welding WPS standards, discovering essential insights and approaches for achieving top-tier welds will be paramount for welders looking for to succeed in their craft and create welds that stand the examination of time.
Comprehending Welding WPS Requirements
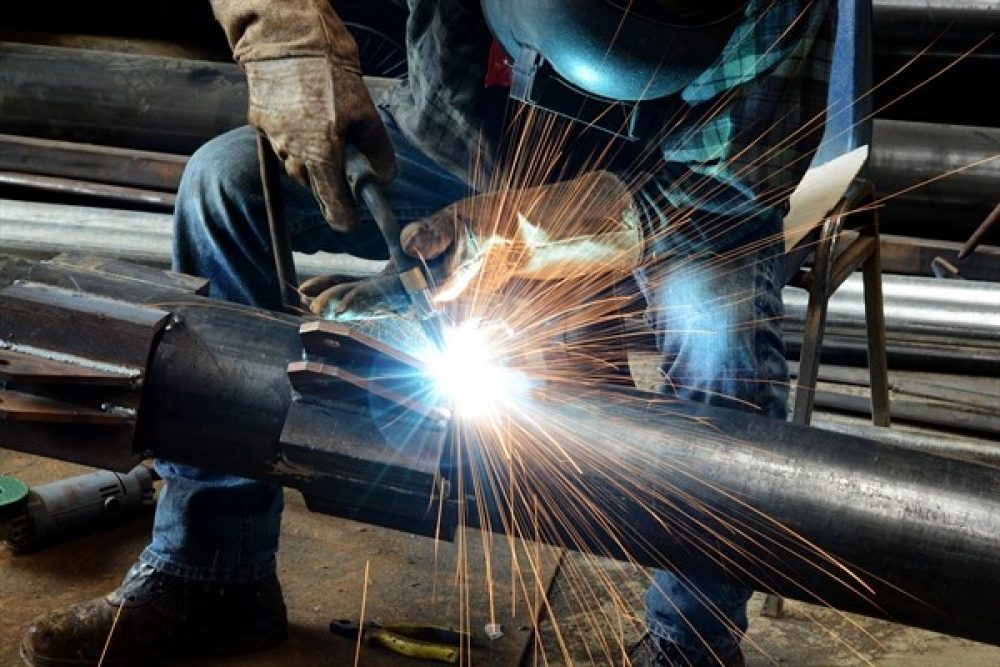
Recognizing WPS criteria is essential for examiners, welders, and engineers associated with welding procedures. By complying with WPS standards, welders can create welds that meet the called for mechanical buildings and architectural stability. Inspectors count on WPS paperwork to validate that welding procedures are being complied with appropriately which the resulting welds are of premium quality. Designers utilize WPS criteria to design welding treatments that make sure the resilience and integrity of welded frameworks.
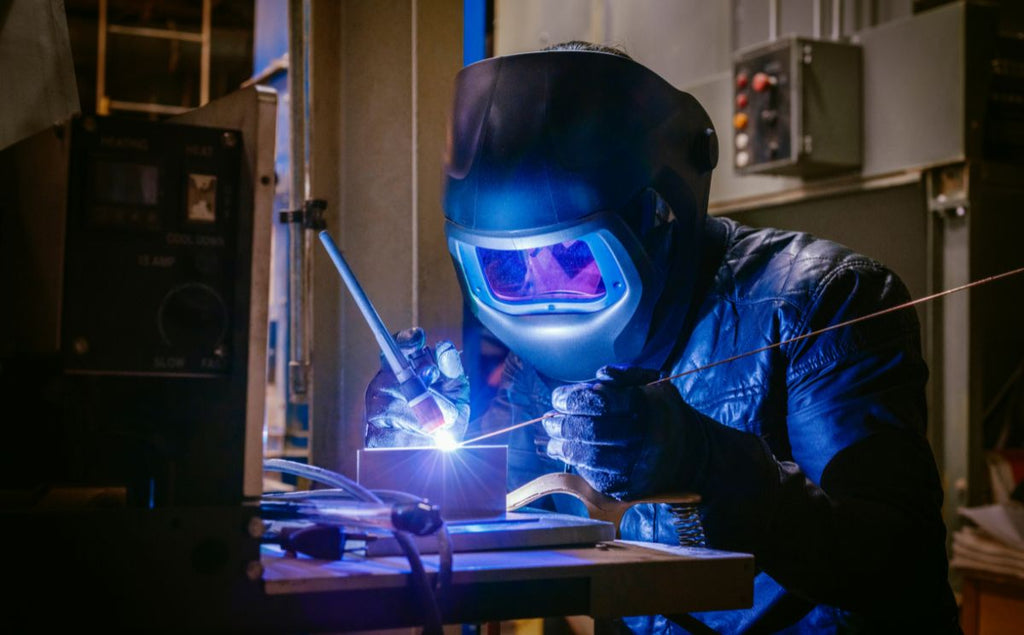

Vital Devices for Top Quality Welds
Understanding welding WPS criteria is crucial for welders to properly utilize the essential devices needed for generating quality welds. One of the most essential tools for quality welds is a welding machine. The kind of welding equipment required depends upon the welding process being used, such as MIG, TIG, or stick welding. Welding helmets are likewise crucial to secure the welder's eyes and face from stimulates, heat, and UV radiation. Additionally, welding handwear covers made of durable and heat-resistant products protect the hands from burns and injuries. Magnets and clamps assist hold the work surfaces with each other safely throughout the welding process, making sure precise and precise welds. Cord brushes and cracking hammers are crucial for cleansing the weld joint before and after welding to eliminate any type of impurities that could influence the high quality of the weld. Lastly, a gauging tape and angle grinder are useful devices for ensuring appropriate positioning and preparing the work surfaces for welding.
Secret Techniques for Welding Success
To accomplish welding success, one must understand the key methods essential for creating high-grade welds. One important technique is preserving the proper arc length. Keeping the electrode at the ideal distance from the work surface is important for producing solid, consistent welds. Additionally, managing the travel rate is paramount. Moving as well swiftly can lead to not enough penetration, while moving as well gradually can bring about too much heat input and prospective flaws. Correct adjustment of the electrode angle is another important method. The angle at which the electrode is held can affect the grain shape and penetration of the weld. In addition, making certain regular gun angle and instructions of traveling is necessary for uniformity in the weld grain. Finally, preserving a steady welding and a steady hand position throughout the procedure is key to achieving accuracy and uniformity in the welds. By mastering these key techniques, welders can raise the high quality of their work and achieve welding success.
Ensuring Conformity With WPS Standards

Additionally, keeping comprehensive records of welding specifications, my response devices calibration, and evaluation results is crucial for demonstrating compliance with WPS criteria. By diligently adhering to WPS criteria, welders can ensure that their work meets the required high quality levels and adds to the general success of the welding project.
Troubleshooting Common Welding Issues
When faced with common welding concerns, recognizing the root cause is critical for reliable troubleshooting. One widespread trouble is the existence of porosity in welds, frequently brought on by contaminants such as corrosion, moisture, or oil. To resolve this, making certain appropriate cleansing of the base steel before welding and making use of the right shielding gas can significantly minimize porosity. Another issue frequently experienced is lack of blend, where the weld stops working to effectively bond with the base material. This can come from insufficient warm input or inappropriate welding technique. Readjusting parameters such as voltage, cable feed speed, or travel rate can assist boost combination. In addition, distortion, fracturing, and spatter are typical welding challenges that can be alleviated via correct joint preparation, regular warmth control, and choosing the ideal welding consumables. By thoroughly understanding these typical welding concerns and their source, welders can effectively troubleshoot issues and achieve top notch welds.
Final Thought
To conclude, mastering welding WPS standards needs a complete understanding of the standards, utilizing important tools, and executing vital methods for successful welds. Guaranteeing conformity with WPS standards is critical for producing top quality welds and preventing typical welding problems. By adhering to best visit this page methods and strategies, welders can achieve trusted and regular outcomes in their welding tasks.
In the realm of welding, mastering Welding Procedure Spec (WPS) standards is a vital element that straight affects the high quality and integrity of welds.When diving into the world of welding techniques, a crucial element to comprehend is the relevance and ins and outs of Welding Procedure Spec (WPS) standards. WPS requirements offer a thorough guideline for welding procedures, making sure uniformity, high quality, and safety in the welding procedure. The type of welding device needed depends on the welding process being made use of, such as MIG, TIG, or stick welding.Attaining welding success with the proficiency click for more info of vital strategies requires a comprehensive understanding and adherence to Welding Procedure Requirements (WPS) standards.